- Can I order gauges with my own logo?
Yes. Marshall Instruments specializes in custom gauges. Minimum order of 100 units typically applies. Contact us for a quote.
View FAQ
- Can I refill my 1.5" liquid filled gauge?
Yes, but to prevent having different layers of fluid we recommend fully draining, rinsing, drying and then refilling.
Once you have fully drained, rinsed and dried out your gauge you can fill it with glycerin, silicone or mineral oil.
- Remove the black rubber fill plug and drain the gauge.
- Rinse the gauge with water, drain and allow to dry. Repeat until you have removed all of the silicone from the gauge.
- Refill with glycerin, silicone, or mineral oil. Leave an air bubble to allow room for the fluid to expand when the gauge heats up.
- Carefully reinstall the rubber fill plug.
View FAQ
- My filled gauge lost some fluid, will it still work?
Your gauge will operate properly with low or no liquid fill.
The liquid helps with vibration and keeps moisture and dirt out of the movement.
You can fill the gauge with mineral oil, glycerin or silicone liquid. Before filling the gauge it is best to empty, rinse and dry the gauge first so you don't get two different fluids mixing (fluids with different viscosity will separate inside the case).
View FAQ
- My liquid filled gauge isn't reading correctly, do I have a faulty gauge?
The gauge is most likely fine and you are seeing the effect of temperature change on the filled gauge.
How do I fix it?
Most of our 0-15 PSI gauges come with a nipple plug. Install the gauge so that the nipple plug is facing up, then cut the nipple off the plug. This will allow the case pressure to be equalized at all times ensuring accurate readings regardless of gauge temperature.
IMPORTANT: DO NOT cut the nipple on the plug if the nipple is not facing up.
If your gauge does not have a nipple plug then see below for instructions on how to vent the gauge.
If your gauge is installed in a position where the fill plug is not facing up then see below for instructions on how to cool the gauge to a known reference temperature.
Only vent the gauge if the fill plug is facing up (air bubble below the the fill plug location). If your gauge is installed in a position where the fill plug is not facing up then refer to the instructions on how to cool the gauge to a known reference temperature.
Venting is easy to do and takes seconds. To vent the gauge carefully push the side of the vent plug (the part under the plug lip) with your thumbnail to equalize the gauge case pressure with the atmosphere (reference pressure). Keep the fill plug vented for 2-3 seconds to ensure the case pressure is allowed to equalize with the outside pressure. Do not remove the plug. See photo below for an illustration of how to vent the gauge:
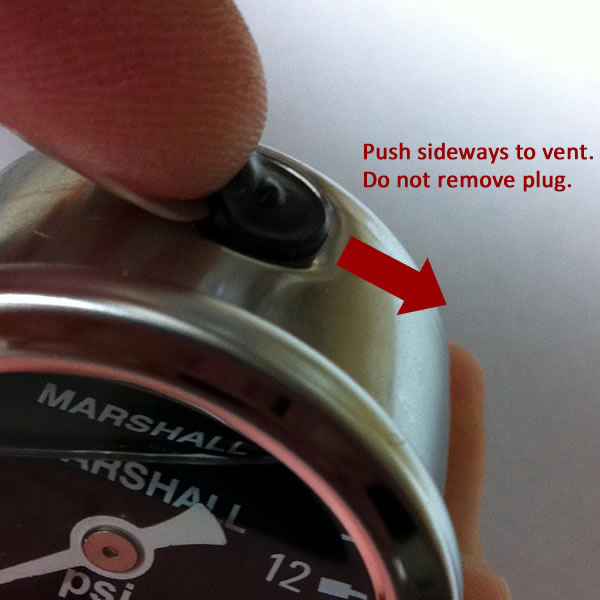
It is OK if some liquid also escapes, just wipe any liquid that escapes off with a cloth. Loss of the liquid fill will not affect operation of the gauge.
How often should I vent the gauge?
To ensure an accurate reading you should vent the gauge whenever taking a pressure reading.
If you can not install the gauge in a position where the fill plug is facing up:
- Before installing warm the gauge up to room temperature (this is your reference temperature).
- Vent the gauge (see "Venting the Gauge" above).
- Install gauge.
- Ensure that the gauge is at the reference temperature when taking a pressure reading. If the gauge is hotter than the reference temperature then wrap a cool wet towel around gauge case to cool the gauge to your reference temperature. If the gauge is cold then wrap a warm wet towel around gauge case to heat gauge up to your reference temperature.
Ensuring that your gauge is at your reference temperature when taking a reading will minimize any pressure offset due to temperature change.
All mechanical liquid filled gauge cases are sealed (to keep the liquid in) so as they heat up pressure will build up in the case (approx 1psi for every 30-40F temperature change). This case pressure exerts a force on the mechanical movement and offsets the actual process pressure. This effect is minimal and typically only noticeable when measuring lower pressures, i.e. on a 0-15 psi gauge.
American National Standards Institute (ANSI) approves American National Standards which include the American Society of Mechanical Engineers (ASME) standard ASME B40.100. This standard addresses venting of sealed gauges within the following section:
Sealed Cases: Liquid filled or not, will exhibit error as a result of exposure to ambient or media temperature different from that at which the case was sealed unless compensation is provided. This error is caused by internal case pressure changes and depends on fill media, extent of fill and other factors. The error is constant over the entire scale, and if the temperature is stable, within limits, it can be corrected by resetting the pointer. An increase in temperature generally causes an increase in internal case pressure with a resulting decrease in indicated pressure. The opposite occurs for a decrease in temperature. For a given temperature change, the percentage of error noted on the gauge is a function or the range of the gauge. If, for example, the temperature increase causes the internal pressure to increase by 3 psi, then on a 30 psi gauge, this will cause a 10% error, whereas on a 0-100 psi gauge, the error will be 3%. For higher ranges, the percentage of error becomes proportionately less.
View FAQ
- Pointer does not rest at zero on 0-15 PSI gauge.
On low pressure liquid filled gauges, such as 0-15 fuel pressure, changes in atmospheric conditions or high temperatures may move the pointer off zero. This is normal. Venting the gauge will return the pointer to zero.
View FAQ
- What are the temperature limits of my gauge?
General guidelines for a silicone filled mechanical pressure gauge with brass internals:
- Min Ambient Temp: -60F
- Max Ambient Temp: 200F*
- Max Process Temp: 150F*
*It is generally accepted that the maximum temperature inside the sensing element of a brass internals gauge should not exceed 150F. This temperature limit is based on the fact that a lead tin solder (soft solder) is commonly used to seal the tip and socket on a bourdon tube type gauge with brass internals. At higher temperatures these joints may loose their strength and fail.
View FAQ
- What is hydraulic shock?
Hydraulic shock occurs when a fluid in motion is forced to stop or change direction suddenly, often due to a valve closing quickly, causing a pressure surge or wave. Hydraulic shock can generate a transient pressure spike many times higher than the normal pressure, enough to overpressure and damage a gauge.
View FAQ
- What is the screw in the connection for?
This is a restrictor screw for pulsation dampening. It helps protect the gauge movement from pressure spikes.
Do not remove the restrictor screw. Make sure the restrictor screw is installed all the way in to the connection and that it is tight.
View FAQ
- What is the warranty on Marshall's 1-1/2" direct mount gauges?
If your gauge has stopped working for one reason or another, we want to make it right for you.
We have two different options available to you:
Option 1: Return Your Gauge for a New Gauge
If you are in the United States and your gauge was purchased within the previous 6 months from an authorized distributor contact us via email with proof of purchase, a photo of your item (showing the problem if possible), and a brief description of your issue. We will send you an RMA number and instructions to return your item for a free replacement. Return shipping fees are applicable if you need the replacement gauge shipped via an expedited shipping method or shipped outside the US.
Option 2: Get a New Gauge at a Smoking Hot Price
If your gauge was purchased over 6 months ago you can get a replacement at a reduced cost of $13 + $5 standard shipping to a US address. Expedited shipping or shipping to a non US address is available for an additional fee.
Contact us via email with a photo of your item, a brief description of your issue, and proof of purchase. We will send you an invoice for a replacement gauge at a reduced price. You can pay with PayPal or credit card if you do not have a PayPal account.
View FAQ
- What is your minimum order?
Minimum order is $300.
View FAQ
- Where can I find the 1.5" filled gauge instructions?
Installation Instructions
- Vent the gauge at a known temperature (i.e. 80F or room temperature) BEFORE installing. This will be your reference temperature to ensure accurate readings. See the following FAQ for more info.
- Gauge connection is 1/8" NPT male. Gauge should only be installed on a 1/8" NPT female connection.
- Use wrench on HEX to tighten/loosen. DO NOT tighten/loosen by turning gauge case. Damage to the gauge may occur and warranty will be VOIDED.
- If possible, mount gauge with fill plug facing up. This makes venting the gauge easier should you need to vent the gauge in the future.
- Test connection for leaks. If a leak is detected, determine the cause of the leak and repair. DO NOT operate if a leak is detected.
WARNING
Failure resulting in injury or damage may be caused by pressure beyond top of scale, excessive vibration or pressure pulsation, excessive instrument temperature, corrosion of the pressure containing parts or other misuse. DO NOT USE ON OXYGEN SERVICE.
View FAQ
- What are the dimensions?
Approximate dimensions of the 1.5" direct mount gauges:
- Case OD: 1.575" (not including plug height)
- Bezel OD: 1.750"
- Length of case and bezel: 1.040" (not incl. fitting)
- Total length including fitting: 1.720"
View FAQ
- What is proof pressure?
ASME B40.100 Bourdon Tube
Proof Pressure Definition
Proof pressure (often times called over pressure) is the maximum pressure a gauge can withstand without evidence of change in
accuracy. Proof pressure may be a semi-destructive test and should not be conducted repeatedly on the same gauge. It may be expressed as a pressure or as a percentage of full scale.
Proof Pressures
1.5", 2" and 2.5" pressure gauges with ranges up to 600 psi have a proof pressure of 125% of span. For ranges above 600psi, the proof pressure is 110% of
span.
Pressure gauges should not operate continuously at the proof pressure limits stated. The
maximum continuous pressure a gauge should be subjected to is 75% of the gauge span per
ASME B40.100.
View FAQ
- How Does Temperature Affect A Filled Gauge?
Changes in ambient temperature affects the accuracy of gauges in several ways.
Range Shift
Range shift is caused by the change in modulus of elasticity of
the bourdon. This effect increases proportionately as the pressure increases. As a general
rule, the loss of accuracy will be an additional 1% of full scale reading for every 50
degree F change in temperature.
Zero Shift
Zero shift is created by the change in physical
dimensions of the various components brought about by the temperature change. This
shift is constant over the entire scale and does not vary with applied pressure.
Maximum Temperature Limits
To ensure longest, possible life and accurate readings,
pressure gauges that have soft-soldered pressure joints should not be exposed to process
or ambient temperatures over 120 degree F. This is especially true of pressure gauges
with liquid filled cases, due to the expansion of the case fill fluid. Long term exposure to
temperatures in excess of 120 degree F may cause discoloration of dials and fill fluids, as
well as hardening of the case seals and possible fill leakage.
Gauges with silver soldered or welded pressure joints should not be exposed to process or
ambient temperatures over 190 degree F.
View FAQ
- What is the Accuracy?
Our gauges have an accuracy of 2% at mid scale.
High and low temperatures affect accuracy on indication. A general rule of
thumb for dry gauges is 1% of full scale change for every 50 degree F change from 75
degree F. Double that allowance for gauges with liquid filled cases.
View FAQ